Optimizing Biologic Formulation Development
Accelerate your biological product with our comprehensive formulation development support. Partner with us for a faster, easier, and more effective drug development process. Our Design of Experiment (DOE) approach integrates everything you need for efficiency and success, including
- Assessing samples under accelerated stress conditions
- Selecting stable drug formulations with sufficient solubility
- Evaluating multiple formulation vehicles
With our informed decision-making framework guiding your biotherapeutic’s development from start to finish, you take advantage of insights from numerous preceding projects and remain focused on the most promising strategies.
Our Process
Our scientists develop multiple drug product formulations side-by-side for enhanced research efficacy and a better understanding of your molecule’s unique components.
With scalability in mind, our team characterizes the best process for manufacturing the bulk formulation and final dosage form. We then handle the transfer to the manufacturing facility.
Once manufactured, materials are then tested for release. Using our central GMP laboratory, we place testing materials on long-term stability to support clinical trials and commercialization. At each appropriate stage, we optimize and validate analytical methods to enhance formulation development and GMP testing.
Formulation Development
Strengthen your next study with critical data from developability assessments. Exclusively designed for early-stage molecules, this stage assesses the primary sequence for chemical liability, solubility and viscosity screening, thermal stability assessments, and propensity for self-association.
Focus on only the most promising formulation boundaries with pre-formulation studies screening encompassing a wide range of pH values and excipient components. We leverage material-sparing experiments with various formulation conditions to generate a pool of promising lead formulations for full assessment.
Make informed decisions and prevent lost time with our ability to identify unsuccessful strategies during liquid formulation assessments. With a straightforward formulation vehicle such as a buffer, stabilizer, tonicifier, or surfactant, we successfully extract insights about each biotherapeutic’s complex structure, composition, ideal stability and product quality.
From these analyses we determine the formulation boundaries of your optimal drug product composition based on the target pH range, and the solubility and stability parameters. We then refine your drug product formulations either through our DOE approach or discrete studies. Testing the resulting samples under accelerated stress conditions reveals the most stable formulations with sufficient solubility.
Finally, our team further refines your optimal formulation composition with accelerated stability testing to differentiate prototypes as well as evaluating storage container compatibility, agitation stressors, and photostability. This testing assesses frozen and freeze/thaw stability to reflect common long-term storage conditions. We also test real time stability under ICH guidelines so you can advance your select lead formulations with confidence.
Achieve speed and reproducibility through custom lyophilization cycles. Our formulation experts create unique lyophilization cycles based on the thermal properties of your drug substance, stability data, and formulation composition.
By pairing our DOE approach and SMART processing technology with formulation selection, we determine and maintain the ideal range for moisture content during storage. This strategy both prevents degradation and enables us to optimize the freezing, annealing, primary drying, and secondary drying process parameters, as well as establish operational parameters for technology transfer. Based on your select materials, our team provides guidance on process design factors including temperatures, sublimination rates, and the speed and reproducibility of reconstitution
Identify dosage and immunogenicity compatibility concerns long before patient use of your biologic. With decades of in-depth industry experience, we understand how to test administration equipment to predict how materials in different IV bags, tubing, syringes, and filters vary between applications.
We assess for any potential risk before chemical composition differences and manufacturing processes cause interactions that interfere with your biotherapeutic and destabilize its efficacy. This precaution is especially important when new safety guidelines increasingly require evaluating additional administration components for clinical entry, such as close system transfer devices (CSTDs).
Overcome the unique development challenges of maintaining biologic stability in injectable formulations. Our team focuses on ensuring compatibility with the device and administration to achieve reliable stability, maintain the desired solubility, and create the ideal product for your target population.
Design a problem-free, comprehensive oral delivery approach to biologics and large molecules. Our experts’ multi-faceted perspectives overcomes frequent challenges with consistent solubility, bioavailability, and permeability, ensuring successful scale-up and patient acceptance.
Vehicle Selection
pH control for solubility and stability
Isotonicity and stability of the drug substance
Prevent aggregation and increase solubility
Stability and improved appearance of lyophilized product
Antioxidants, cryoprotectants, viscosity modifiers, etc. to improve stability in solution and/or lyophilized product
Progress from Formulation to Manufacturing with Advanced Technologies
Effective & Robust
We specialize in developing effective, stable, and easy-to-manufacture biologic formulations. From the first step to the last, our team approaches each formulation project with the final commercial product in mind. Across every development program, we prioritize:
- Effectively preserving the API and controlling delivery through the intended route of administration.
- Ensuring the product is safe to use, tolerable to the patient, and comfortable at the site of administration.
- Compatibility with our technologies and processes, as well as scalability to a wide range of standard processes available within commercial CMOs.
- Effectively preserving the API throughout manufacturing, distribution, product shelf life, and administration.
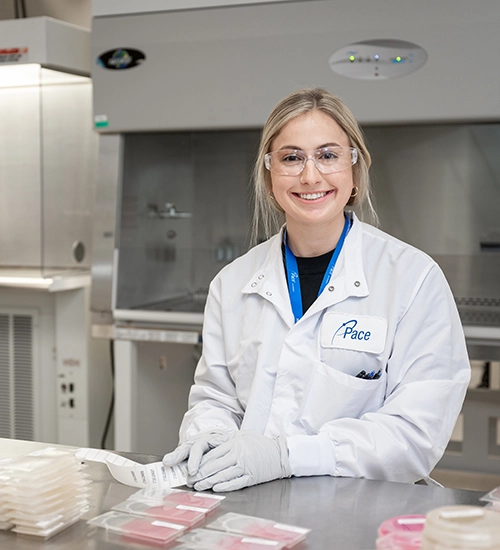
Developing a Hydrogel Microneedle Array Patch
Microneedles, or micro array patches (MAPs), are an evolving technology that is set to change the way we think about transdermal drug delivery systems. MAPs provide a method to bypass the stratum corneum barrier, creating new opportunities for a large variety of compounds to be delivered through the skin.
Hydrogels are a subcategory of MAPs that can be custom tailored to fit the needs of various delivery strategies, particularly those that require extended or controlled release. Careful planning needs to go into designing a hydrogel MAP, and seemingly trivial aspects should not be underestimated. Learn more about these innovative dosage forms and delivery technologies in our whitepaper.
Integrated Laboratory Services
When your team needs additional CDMO support, our scientists are ready. Our state-of-the-art facilities and highly trained experts can add power to your project.